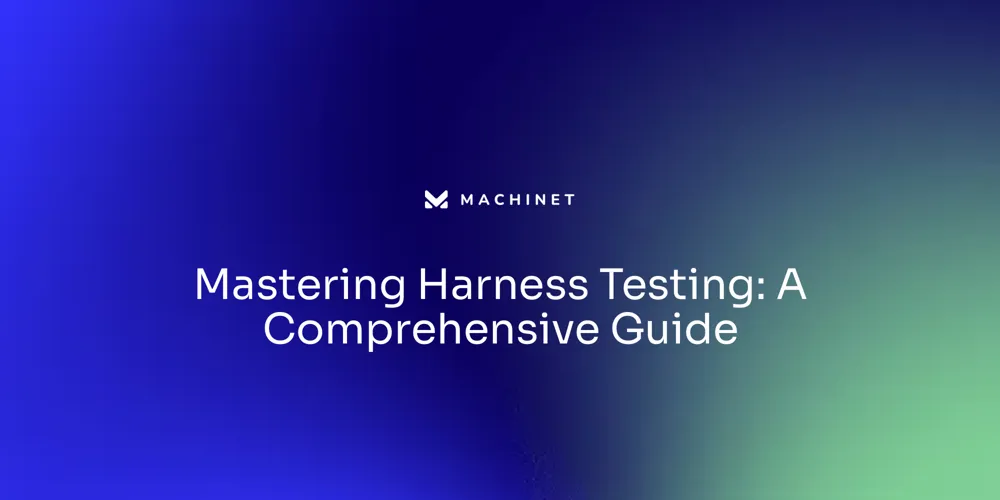
Table of Contents
- What is Harness Testing?
- Types of Harness Tests
- Gear Requirements for Harness Testing
- Step-by-Step Guide to Harness Testing
Introduction
Harness testing plays a crucial role in ensuring the safety of workers operating at dangerous heights in industrial mountaineering. With the development of innovative materials, such as carbon nanotube-based foam, there is a continuous effort to enhance protective gear and reduce the risk of equipment failure.
This article will explore the different types of harness tests, the gear requirements for testing, and provide a step-by-step guide to conducting thorough harness testing. By following a meticulous approach to equipment maintenance and testing, organizations can safeguard the well-being of climbers and improve overall safety in high-risk environments.
What is Harness Testing?
Inspecting the integrity of climbing harnesses is an essential practice in the field of industrial mountaineering, where the safety of workers operating at dangerous heights is paramount. Research indicates that safety ropes, often seen as the weakest link in fall protection systems, should undergo visual checks before each use and require periodic replacement—every five years for individually assigned equipment and annually when shared among employees. This meticulous approach to equipment maintenance is critical, given the high stakes of industrial climbing professions, where physical fitness, skill, and strict adherence to safety protocols are non-negotiable.
The recent development of a new, carbon nanotube-based foam that absorbs kinetic energy more efficiently than traditional materials holds promise for further enhancing protective gear, such as helmet liners, possibly reducing the incidence of concussions in high-impact scenarios. This innovation underscores the industry's ongoing commitment to advancing safety technology in response to the inherent risks of working at height. As such, harness testing not only confirms the reliability of the gear but also serves as a cornerstone in the broader effort to safeguard the well-being of climbers against the consequences of equipment failure.
Types of Harness Tests
Quality assurance for exosuits is paramount, considering their role in enhancing workforce well-being and productivity. To ensure these innovative garments meet the highest standards, a comprehensive testing protocol is essential. Visual inspections are a fundamental part of this process, where trained personnel meticulously check for any irregularities or signs of wear that might compromise the suit's integrity.
Additionally, physical stress tests are conducted to simulate the real-world strains an exosuit might endure. This involves subjecting the suits to forces and conditions they would typically face while being worn by workers. Load tests further contribute to the assessment, measuring the exosuit's ability to handle weight and pressure without failure.
These methods not only safeguard the user but also serve to evaluate the long-term financial benefits that come from reducing workplace injuries, as indicated by the use of ROI calculators like the Apex 2. It's a meticulous process that mirrors the careful evaluation researchers apply to studying stress in wild horses, as observed in the cortisol level studies on Sable Island. By applying a similar level of diligence to exosuit testing, organizations can ensure both the safety of their employees and the economic efficiency of their operations.
Gear Requirements for Harness Testing
To execute harness testing with precision and ensure quality control, the selection of robust equipment is paramount. A state-of-the-art testing apparatus, such as the OmniTest, designed by Mecmesin, is a prime choice for this purpose. It's engineered to perform an array of static tensile and compressive tests on materials like plastics, rubbers, and metals, providing quantitative results with high repeatability.
The OmniTest boasts a user-friendly interface with live load and length readings, and precision manual crosshead positioning, which is essential for accurate testing. The incorporation of Enhanced Load Sensors (ELS) guarantees exceptional load accuracy, with a reading accuracy of 0.5% and a resolution of 1:50,000, allowing for a broader range of tests without the need to switch sensors. This meticulous approach to testing is critical, especially as the industrial mountaineering industry notes the safety ropes as the weakest point in fall protection systems, necessitating regular replacement and visual inspections before each use.
Moreover, it's important to ensure that the support equipment itself is not causing issues, as per the recommendations. By turning off the support equipment without affecting the equipment under test, or vice versa, you can determine the source of any problems. This is crucial, as the integrity of support equipment is also a potential fault point.
To further facilitate effective testing, authorized entrants must be versed in using the monitoring equipment and must participate in the initial monitoring to detect any hazardous conditions. A clear communication system must be established between entrants and the attendant, which is a vital safety measure in the event of an emergency. With the right equipment and procedures in place, harness testing can be conducted efficiently, contributing to enhanced safety and compliance with industry standards.
Step-by-Step Guide to Harness Testing
Ensuring the integrity of manufacturing equipment is crucial, especially when considering pivot joint testing. The process begins with a meticulous visual inspection of the equipment.
This is not just a cursory glance; it requires a keen eye for detail, especially in areas that typically experience wear and tear. Signs of damage or deformation are red flags that need immediate attention.
Following the visual inspection, the equipment undergoes rigorous physical stress tests. These tests are not arbitrary; they simulate the conditions the equipment will face in a real-world setting.
Pressure and force are applied to different parts to gauge their resilience, mimicking the regular stresses they will encounter. Load tests are equally critical.
The equipment is connected to a testing rig where it's subjected to the maximum weight it's expected to manage. This isn't done haphazardly but rather gradually, to ensure the equipment can handle the load without compromise.
Documentation throughout this process is not an afterthought. It's a meticulous record that captures every detail of the testing phase—date, time, results.
This documentation isn't just for keeping tabs; it's a critical component that speaks to the manufacturing excellence of the equipment. As Boyd's insights reveal, meticulous planning and control are imperative in a manufacturing landscape where variety is the norm and each product may differ from the next. In light of recent studies, like the one led by Rachel Murray, which delve into the impact of equipment design on biomechanics, it becomes clear that the quality of testing equipment can have far-reaching effects. These studies underscore the importance of precision in design and testing, as even seemingly minor changes can significantly influence outcomes. The importance of comprehensive testing and documentation cannot be overstated. It's a testament to a commitment to quality and safety, echoing Dr. David Bolt's emphasis on the vetting process in determining a horse's health. Similarly, manufacturing equipment must undergo a 'vetting' process to ensure it stands up to the demands placed upon it, safeguarding not just the equipment but also the people and processes that rely on it.
Conclusion
Harness testing plays a crucial role in ensuring the safety of workers operating at dangerous heights in industrial mountaineering. The recent development of innovative materials, such as carbon nanotube-based foam, highlights the industry's commitment to advancing safety technology and reducing the risk of equipment failure. There are different types of harness tests that organizations can utilize to enhance safety.
Visual inspections and physical stress tests help identify any irregularities or signs of wear that might compromise the integrity of climbing gear. Load tests assess the equipment's ability to handle weight and pressure without failure. These meticulous testing methods not only safeguard climbers but also contribute to long-term financial benefits by reducing workplace injuries.
To conduct thorough harness testing, it is important to have robust equipment like the OmniTest, which performs an array of static tensile and compressive tests with high repeatability. The selection of reliable gear is essential for precise and accurate testing. A step-by-step guide to harness testing involves a meticulous visual inspection, rigorous physical stress tests, and load tests that gradually apply maximum weight.
Documentation throughout the testing process is crucial for record-keeping and manufacturing excellence. In conclusion, by following a meticulous approach to harness testing and equipment maintenance, organizations can safeguard the well-being of climbers and improve overall safety in high-risk environments. Harness testing serves as a cornerstone in the broader effort to enhance safety technology and protect against the consequences of equipment failure.
Upgrade your harness testing with the OmniTest for precise and accurate results.
AI agent for developers
Boost your productivity with Mate. Easily connect your project, generate code, and debug smarter - all powered by AI.
Do you want to solve problems like this faster? Download Mate for free now.